電着や焼付け塗装などの加熱・冷却処理を行うと、ホワイトボディ(BiW)のボディサイドアウター部分に座屈や波打ちといった恒久的な塑性変形が発生することがあります。このような不具合は車両の品質に大きな影響を与えます。一般的に、変形が生じる原因として以下の要因が考えられます。
- 加熱や冷却を通じて、サイドアウターパネルとインナーパネルの間に局部的な温度差が生じると、冷却後にアウタースキンパネルのサーフェスが不均一に変形し、不具合が発生することがあります。
- ハイブリッドBiWでは、鋼材とアルミニウムの線膨張係数の違いが、加熱や冷却を繰り返すことで、鋼材のサイドアウターパネルのサーフェスに局所的な塑性ひずみが生じることがあります。
鋼材とアルミニウムのハイブリッドBiWでは両方の不具合が同時に生じる可能性があり、鋼材またはアルミニウム単一のBiWよりも不具合が頻発する傾向にあります。トライアウトや生産段階で対処する場合、複数部門による広範な検証対策が必要となるため、特に効率が悪くなります。
しかしCAEシミュレーションツールを活用して初期の製品開発段階で不具合を識別し、検証を行えば、これらの不具合を効率的に排除することができます。このように後工程を見越した対策を講じることで、量産時の不具合やその深刻度を大幅に軽減できます。
本稿ではAutoForm Assembly 熱硬化モジュールを活用した不具合の解析およびその回避策についてご紹介します。
AutoForm Assembly 熱硬化モジュールを活用した焼付け塗装のひずみ解析
シミュレーションでは、結果に大きな影響をおよぼす加工条件を、材料カードで正確に設定および定義する必要があります。
- 線膨張係数はAutoForm Assemblyによる焼付けのシミュレーションにおいて、最も大きな影響があるパラメータです。
- 熱伝導率は、材料の熱伝導のしにくさを示します。
- 対流熱伝達率は、流体と固体のサーフェス間の熱伝達能力を表します。これは焼付けのシミュレーションにおいて、シミュレーション対象物と周囲環境に対して定義します。
前処理
解析の前処理、つまりシミュレーション設定には複数の工程が必要となります。
まず材料の板厚方向、材料の板厚、材料モデル、熱力学パラメータなどを設定します。本稿の対象であるインポート済みのサブアセンブリを図1に示します。
工程計画ステージでは、工程数や各工程で組み立てる部品/サブアセンブリを決定し、図2に示すとおりアセンブリシーケンスツリーを作成します。
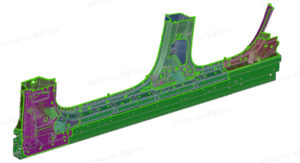
図1:AutoForm Assemblyにインポートしたサブアセンブリ
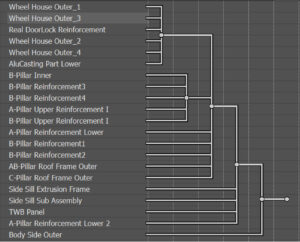
図2:アセンブリシーケンスツリー
組付け治具への設置と固定を行う際には、各部品/サブアセンブリの接合時に安定性が担保されるように、工程ごとに設置順序(図3)、設置方向、位置決め、クランプの方策を検討する必要があります。
次に接合と接着です。本件ではスポット溶接、接着(図4)、FDSを使用しますが、FDSはまだソフトウェアに実装されていないため、代替モデルとしてリベットを使用します。
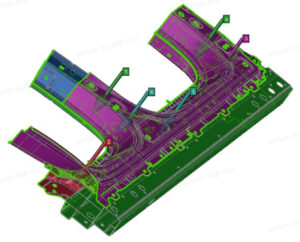
図3:設置順序
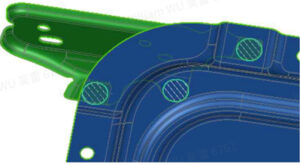
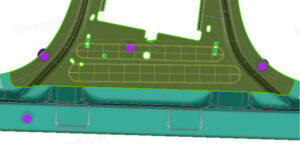
図4:シミュレーションで使用する接着
シミュレーションでは最後に熱力学パラメータ(線膨張係数、熱伝導率、対流熱伝達率)を部品や材料ごとに定義します。熱伝達率は、鋼材で45mW/mmk、鋳造アルミニウムで220mW/mmk、熱間プレス成形の鋼材では23.3mW/mmkに設定します。 また本体と周囲環境間の対流熱伝達率は0.02mW/(mm^2・K)に設定します。 さらに焼付け時の加熱時間と温度保持時間は、実際の加工条件に合わせて設定します。
シミュレーション結果の考察
サイドパネルの変形をシミュレーションする場合、その結果の品質は、主に変形の程度とバーチャルオイルストーンの性能によって決まります(図5)。

図5:サイドアウターパネルの変形
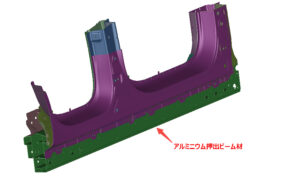
図6:ボディサイドのアセンブリにおけるアルミニウム押出ビーム材
サイドアウターパネルの下側部分に1.9mmの著しい膨張が見られますが、これはアルミニウム押出ビーム材の線膨張係数が他の鋼材パネルよりも高いことに起因します(図6)。 この変形は加熱や冷却から生じたものです。もし塑性変形の値が滑らかな勾配をもって変化し、局所的に急激なばらつきを持たなければ、実際の車両では面ひずみはほとんど検出されません。そのため、この塑性変形の量を構造的な剛性の指標として、構造設計の初期段階における剛性の最適化のために使用することができます。
図7はバーチャルオイルストーンの結果を示しています。Bピラー下部の両端で最大0.17mmという急激な値が確認されました。これらの結果から、この領域で波打ちが生じていると結論づけることができます。
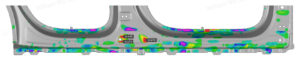
図7:X方向のバーチャルストーニングの結果
図7の結果は加工条件下でのへこみや波打ちといった面ひずみの可能性を示唆しています。したがって、この結果を焼付けによる変形の影響を受けた面精度の最終評価の指標として使用します。
シミュレーション結果の検証
図8および図9では焼付けの前後における実際のアウターパネルを比較し、変形傾向とシミュレーション結果との相関性を紐解きます。
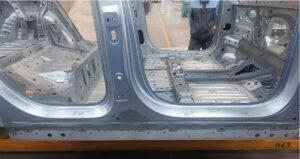
図8:焼付け前のBiW
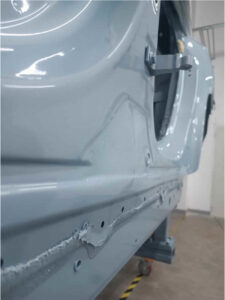
図9:焼付け後の状態
Bピラー下端付近では膨張による変形が検出され、図5が示す傾向と一致します.
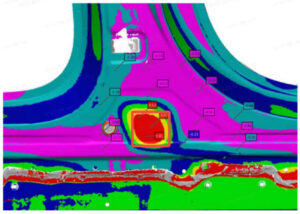
図10:焼付け後のBピラー部分のスキャン結果
図10にスキャン結果が示されているとおり、焼付け後にBピラー領域には正規寸法からの偏差が生じます。図5と比較すると、膨張による変形は傾向と分布の両方でシミュレーション結果と高い相関性があり、焼付けによる変形のアセンブリシミュレーションは非常に高精度であることがわかります。
まとめ
サイドパネルの焼付けによる変形は、自動車業界における長年の課題です。この不具合に対処するためには、既存の解析ツールでは限界があり、構造的な剛性の設計がどのように影響するかを効果的に評価できませんでした。従来は、余分な補強材を追加するなどの対応がとられてきましたが、これにより効率が低下し、コストも増加していました。しかし熱硬化のシミュレーション技術が採用されたことで、サイドパネルの焼付けによる変形を正確に評価できるようになり、構造設計を効果的に改善することが可能になりました。この手法により、車両製造時の不具合に関連するリスクが大幅に低減され、余分な補強材のコストも削減可能となりました。
さらにこのタイプの解析は、複数の材料タイプを使用したドアなどの他のサブアセンブリにも適用できるため、潜在的なメリットはさらに広がります。
NIO社のコメント
デジタルシミュレーション担当部署のリーダーであるトゥ氏は、このような不具合対応を広範に適用できる可能性について示唆しています。「ハイブリッドBiWを扱う多くの企業が焼付けによる変形の不具合に悩まされています。AutoForm Assemblyを活用して初期段階から対策を講じることで、トライアウトや量産における潜在的な損失を削減することができます」
著者について
シャオウェン・トゥはデジタルシミュレーション技術部を率いるほか、NIO社フォーサイト製造技術部門に属するプレス成形工程に精通した技術者でもあり、自動車業界で22年の経験と数値シミュレーション技術に精通しています。
ペンペン・リュウ・シャオキアン・パンは、NIO社フォーサイト製造プロセスイノベーションセンター部門の主要メンバーです。
ジュレイ・ウー・レイ・リューは、NIO社製造技術(BiWシステム)部門を代表するメンバーの一員です。