BiWアセンブリのDX化~新たなアプローチ”VARプロセス”とは~
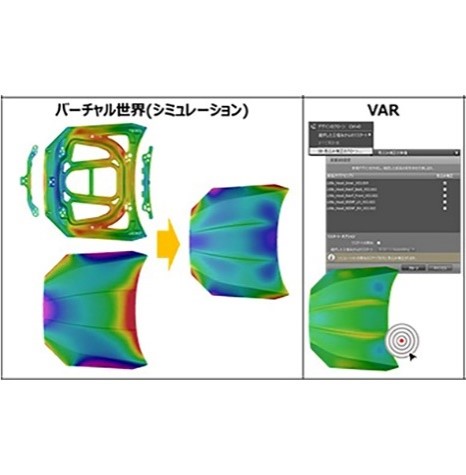
BiWアセンブリのDX化~新たなアプローチ”VARプロセス”とは~ 過去のニュースレターでも何度かご紹介してきたAutoForm Assemblyソリューションですが、今回はAutoForm Assemblyを使った新しいアプローチ:VARプロセス(バー・プロセス:詳細は下記)をご提案いたします。 唐突ですが… 現在のBiWアセンブリへの取り組みは、プロアクティブとリアクティブのどちらだと思いますか? “プロアクティブ” トライアウト時の問題を最小限にするために、結果を予測・シミュレーションし、プロセスを改善する。 OR “リアクティブ” トライアウトを待って、その結果に基づいて工程や部品を調整する。 もしプロアクティブな取り組みが必要な場合、どんなツールとアプローチが必要なのでしょうか? 私たちの答えは、AutoFormとVARプロセスです。 VARプロセスとは 図1のフード・コンポーネントを使って、現在の典型的なアプローチとここでご紹介するVARプロセスの概要と違いをご説明いたします。VARプロセスは、プレス単品の公差保証ではなく、BiWアセンブリ・コンポーネントの寸法精度が公差内に入るような目標形状を工程検討段階で新たに定義することで、より早く、低コストでプレス成形とBiWアセンブリ工程を仕上げることを可能にするものです。 図1. 工程検討 – フード・コンポーネントの見込み戦略 まずは、図1のa. 現在の典型的なアプローチで何が起こっているかを分析してみます。ここでは寸法精度が公差内に収められたフード・アウター・パネル、フード・インナー・パネル、インナー・パネルの補強部品2つの計4部品があります。プレス成形担当者としては目標を達成しているケースです。しかし、BiWアセンブリ工程で補強部品をフード・インナー・パネルに接合し、アウター・パネルにヘミング後、アセンブリ後の公差内に収まらない結果になりました。…なぜでしょうか?その原因として、次の2点が考えられます。 自重の影響:コンポーネント内のすべての部品重量が寸法測定治具上に負荷され、 自重を負担するインナー・パネル部品に作用した。 工程の影響:スポット溶接などの接合工程とヘミング工程で生じる応力が寸法精度に影響した。 などがあります。これらの要因への対応策として、以下が一般的です。 アセンブリ後の変形を考慮した部品形状の決定。 アセンブリ工程の修正。 通常、これらの問題は実際にBiWアセンブリ工程のトライアウトを行うまで発見することができない上に、現場でさまざまな選択を迫られることになります。ヘミング前の部品の接合状態を調べて部品のクランプ条件を修正したり、ヘミング工程を調整したりします。それでも問題が解決しない場合は、部品形状を補正して精度を上げるしかありません。フード・コンポーネントでは、通常インナー・パネルが形状補正の対象になります。しかし、どのような部品形状にするのが良いのでしょうか?それをどのように決めれば良いのでしょうか?これまでの経験やノウハウ、試行錯誤の組み合わせを用いて、なんとかモノにすることになりますが、この“従来の方法”では“時間とコスト”がかかってしまいます。 そこで、AutoFormの新しいアプローチである、 VARプロセスの出番です。図1のb. VARプロセスをご覧ください。4つの部品それぞれのシミュレーション結果を活用して(*シミュレーション結果がない部品はCAD-0データを使用します)、AutoForm AssemblyでBiWアセンブリ工程をシミュレーションします。予想通り、寸法精度が公差内に収まらない結果になりました。そこで、下記の手順で工程検討します。 どの部品の形状補正をするかを、AutoForm Assemblyを使って決定する。 1.で決定した部品の、新しい目標形状をAutoForm Assemblyで決定する…これが、バーチャル・アセンブリ・リファレンス(Virtual Assembly Reference):VAR さらに、AutoForm Formingを使って部品形状を得るためのプレス成形工程で、金型の見込み補正作業を行う。 この新しい目標形状を他の部品とアセンブリすることで、フード・コンポーネントの寸法精度が公差内に収まり良い結果となります。BiWアセンブリ工程を考慮したこの新しい目標形状:VARを活用することで、より早く、低コストのプレス成形とBiWアセンブリ工程を仕上げることができます。これはコストがかかる現実世界ではなく、バーチャル世界のソフトウェアによるエンジニアリングでのみ実現可能なものと考えております。 BiWプロセス・チェーンにおけるVARプロセス AutoForm Assemblyは初期段階のフィージビリティ・スタディ、プロセス・エンジニアリング、BiW量産までのBiWプロセス・チェーン全体をサポートします。BiWアセンブリ工程にAutoFormソリューションを導入することで、車体製造工程を深く理解し、部品公差やアセンブリ工程設計を迅速に評価し、寸法偏差の要因を特定することができます。また、効果的な対策を取っていくための検討を効率的に行うことができます。その結果、BiW全体の寸法精度を達成することができます。 図2. BiWプロセス・チェーン 図2のプレス成形とBiWアセンブリの間にある赤いゾーンでは、何が行われているかを考えてみます。プレス成形の領域で行われているタスクと、BiWアセンブリの領域で行われているタスクがあります。これは、関連するプロセス・チェーンの中で、異なる担当者が異なる仕事を行う可能性があることを意味しています。各部門やシステムがそれぞれ自己完結し、部門やシステム間の連携がうまくいかないサイロ化(図2左下)の状態になると、業務効率の低下、意思決定スピードの鈍化、不要なコストの発生など、多くのデメリットがあります。システムのサイロ化解消には、データ統合による一貫したデータ・マネジメントが必要です。また、ここでご紹介しているVARプロセスで最大限の効果を得ていただくためには、以下の条件が必須と考えています。 部品にフォーカスする 良好なコミュニケーション コラボレーション ここからは、現在のワークフローでは得られない有益な情報を、VARプロセスを使ってどのように得るかを考えていきたいと思います。 図3. CAD-0データを用いたBiWアセンブリ工程の […]