Starq Y-Tec社ではホワイトボディのアセンブリ工程を正確に予測し、トライアウト回数を大幅削
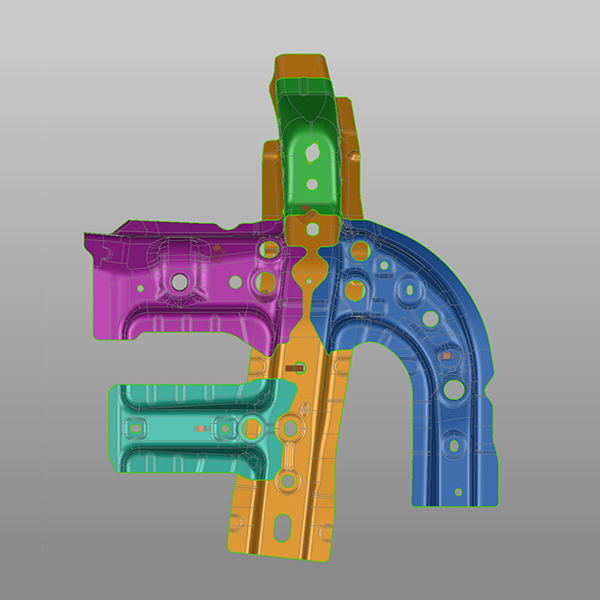
概要 先んじて実施された イタリアFontanaグループとの共同プロジェクトにおいて、プレス成形工程およびアセンブリ工程の解析ソフトウェアであるAutoFormが非常に高精度であることが確認されました。その後、マツダやBYDのTire1サプライヤであり、BiWコンポーネントのプレス成形およびアセンブリを請け負う中国Starq Y-Tec社の現場にて、新たな検証プロジェクトが実施されました。 本稿ではStarq Y-Tec社がAutoForm Assemblyを活用し、最終製品に至るまでの工数を大幅削減した事例について紹介します。 課題 Starq Y-Tec社は大手メーカーを顧客に有する単品部品のプレス成形およびアセンブリのサプライヤです。当時はアセンブリ工程をシミュレーションできるデジタル・ツールは使用しておらず、すべてアナログで組立作業を行っていました。そのためアセンブリ工程で生じうる不具合を事前に特定できる手段は何もありませんでした。 ある顧客のフロント・サイド・メンバーを製作する中で、アナログな作業には多くの無駄な試行錯誤が伴うという気づきがありました。 単品のプレス部品は仕様と完全一致しているとは言い難くも、基準形状とは大差ないものでした。プレス成形部門での作業時にはスプリングバックの問題に対応しましたが、部品が仕様の範囲内に収まると、アセンブリ部門による組立作業に移行しました。 しかしプレス部品を組み立てると、部品が設計通りにはまらないことが判明したのです。そこでエンジニアリング部門まで部品を戻し、デザインの見直しが行われました。部品設計の修正からプレス成形やトライアウトまで含めると、この見直し作業には約2~3週間を要しました。 それでもトライアウトでは十分な結果を得ることができませんでした。そして最終的に仕様が満たされるまで、この一連の作業を何度も繰り返すことになったのです。ここでご留意いただきたいのは、単品のプレス部品は初期の設計から公差に収まっていたという事実です。 Starq Y-Tec社副社長Li Qi氏は次のように述べています。「デジタル・ツールを活用してアセンブリの不具合を事前に予測しなければ、最終段階まで不具合対応に追われることに気づきました。初期段階にて多大な労力をかけて単品部品を公差に収めたにも関わらず、後期段階ではその部品を組み付けることができず、単品部品の設計やトライアウトからやり直しました。これには莫大なコストと時間がかかります」 プレス成形やホワイトボディのアセンブリにおいて、このような事例は頻繁に生じています。OEMでも部品に修正を加えて最終アセンブリに対応したといった事例も多くあります。またアセンブリ部門による部品の組み付けが上手くゆかないと、エンジニアリングやトライアウトの部門に立ち戻り部品設計を見直す必要があるため、アセンブリ部門で生じた不具合の対応に追われることに不満を感じる場合もあるようです。 不具合への対応策 アセンブリ部門では不具合を検出すると、以下のタスクを繰り返しながら工程を修正してゆくことで、アセンブリの改善を図りました。 クランプの位置や順序の変更 溶接の位置や順序の変更 単品部品のさまざまな修正 不具合が解消されるまで、このトライ&エラーのループを4回以上も繰り返す必要がありました。1回あたり2~3週間を要するため、この方法には膨大な時間がかかるだけでなく、非常に複雑で非効率であることも明らかです。 開発期間の長期化、コスト上昇や生産遅延、最終製品や金型の品質低下といった問題が生じるだけでなく、生産が遅延しないよう従業員が残業を強いられるなど、時間やコストに過剰な負担が生じることは言うまでもありません。 このように計画性がない生産活動の中で軽視されがちなのが、実際の作業にあたる担当者の心の健康です。明確な目的が示されずに仕事量のみが急増することで疲労や不満が増大し、士気や自信も低下します。エンジニアリング、アセンブリ、トライアウトの部門間で業務に対する責任の擦り合いが生じ対立が深まると、さらに悪影響が広がります。 このような負の関係性は、残念ながら多くの生産現場で見られるようです。しかしながらデジタル・シミュレーションを活用すれば、アセンブリを良好に進めるためにどのような修正を行うべきかが明確になり、このような部門間の対立もすぐに解消されるでしょう。 AutoFormソリューション Starq Y-Tec社の上層部は、アセンブリの不具合を事前に予測できれば、このような問題を回避できると判断しました。常に納期短縮を目標に掲げ、不具合の対応に数週間はおろか数日の猶予すら嫌がる大手メーカーの顧客満足度を高めるには、より迅速で信頼できるソリューションが必要でした。 そしてStarq Y-Tec社ではAutoFormソフトウェアによるアセンブリのシミュレーションについて、検証プロジェクトを立ち上げました。このプロジェクトでは2段階の検証を行いました。 アセンブリ工程で生じうる不具合や課題をAutoFormソフトウェア上で正確に再現できるかを検 証。またシミュレーションの実行前には実部品を測定。使用した部品は5個のコンポーネントで構成 されたフロント・サイド・メンバー。材料はSPCM980YL-55/55、板厚は1.8mm。 AutoFormシミュレーション結果と実部品の実測値を比較し、シミュレーション精度を検証。 結果 AutoFormシミュレーション結果は、実際のアセンブリ部品の実測値に非常に近いことが判明しました。 比較を行うため、合計104カ所で測定を行いました。差異が0.5 mm未満であったのは80カ所、そのうち56カ所は0.3 mm未満でした。 残りの24カ所は差異が0.5mm以上でしたが、1mm以上の差があったのはわずか6カ所です。 アセンブリのシミュレーションでは、実際のアセンブリ部品と非常に近い結果が得られました。50%以上が0.3mm以内、74%がアセンブリ部品の0.5mm以内でした。 シミュレーションを使えば、アセンブリ工程における不具合を高い精度で予測することができます。しかもすべて比較的短時間で行えます。 ソフトウェアをより広範に活用すれば、工程のバーチャル・モデルを作成し、実際の製造現場で実施しているトライアウトの回数を大幅に削減することすら可能になります。 唯一無二のAutoFormソリューション AutoFormには、競合他社にはない以下3点の優位性があります。 あらゆるアセンブリ工程のモデル作成工程を詳細に表現するために必要な幅広い金型と設定を備えています。そのため、さまざまなアセンブリ工程のモデルを作成することができます。 […]