LINGYUN China
サイドシル・アセンブリは、安全や品質を担保する上で重要な自動車部品です。安全性の観点から、主に超高張力鋼材を使用し、また溶接ポイントも多数あります(図1)。そのためサイドシル・アセンブリの寸法を調整することは非常に難しいとされています。本稿ではサイドシル・アセンブリのトライアウト工程を円滑に進める上で、どのようにAutoForm Assemblyを活用できるかご紹介します。
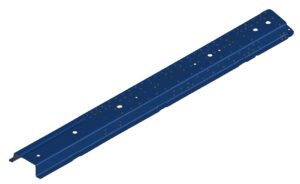
図1: 溶接ポイントの分布
このアセンブリには128箇所もの溶接ポイントがあり、溶接は6工程で実施します(図2)。
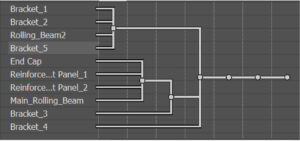
図2: 溶接計画
従来通りにトライアンドエラーを繰り返しながら何度か溶接のトライアウトを試しても、深刻な寸法上の不具合は解消されませんでした。最も顕著なものは端部の著しいねじれで、片側で+2.5mm、もう一方では-1mmの偏差が確認されました(図3)。
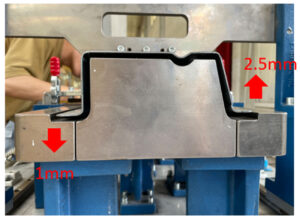
図3: 数回のトライアンドエラー後の寸法偏差
この結果から、従来のトライアウトだけではアセンブリを適正に実行することは難しいと判断しました。そこでAutoForm Assemblyを活用し、工程の数値解析を行うことになりました。
ステップ1:すべてのパネルを個別にスキャンし、そのデータをもとにアセンブリ工程をシミュレーションすると、非常に高精度な結果が算出されました(図4)。
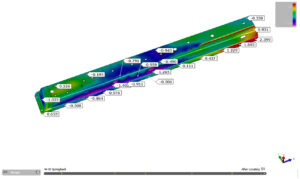
図4: スキャンしたデータを活用したシミュレーションの結果
バーチャルアセンブリの解析中、スキャンしたパネルを合わせる際に2つの不具合が特定されました。まず、エンドキャップと呼ばれる部品の単品寸法精度の不良により、フィレット部分でエンドキャップとメインローリングビームに干渉が生じていました(図5)。次に、ローリングビームと小型ブラケットの合わせ面には約0.8mmの意図的に設計されたギャップがありますが、これが最終アセンブリではひずみの原因となりうることが確認されました(図6)。
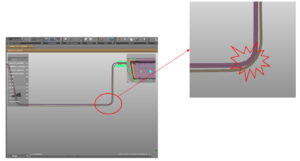
図5: エンドキャップとローリングビームの干渉
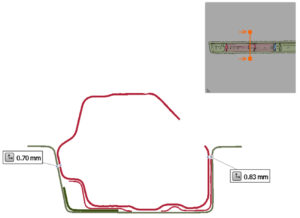
図6: 意図的に設計された合わせ面のギャップ
ステップ2:2つの部品パネル(メインローリングビームとエンドキャップ)を選択し、AutoForm Assemblyにて見込み補正を実行しました。最終的な補正量と結果を図7と図8に示します。
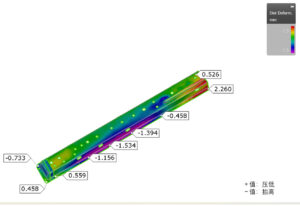
図7: 見込み補正量の分布
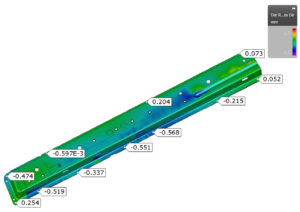
図8: 見込み補正後の結果
シミュレーション結果をもとに、部品設計と個別のパネルに3つの修正を施しました。
- ローリングビームとエンドキャップの見込み補正
- エンドキャップの干渉部分の修正
- 小型ブラケットの公差を調整し、実パネルの寸法を修正することで、合わせ面のギャップを最小限に抑制
その結果、ほぼすべての寸法が±0.8 mmの公差内に収まり、溶接アセンブリの不具合はほぼ解消されました。テストポイントの1箇所に約1 mmの偏差(図9)が生じましたが、この程度の寸法誤差は自動車製造に障りはないため、これ以上の最適化は必要ないと判断しました。
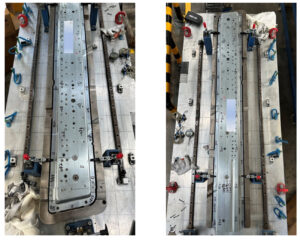
図9: 是正処置を施した後の最終アセンブリ
結論:
- AutoForm Assemblyは、複数の超高張力鋼材を使用したサイドシル・アセンブリの解析に効果的に活用できます。
- パネルの寸法不良や溶接ポイントの密集に起因するねじれを予測および解析できます。
- サイドシル・アセンブリのトライアウト工程を円滑に開始する上で、AutoForm Assemblyから有意義な情報を得ることができます。